Lean Construction is more than a methodology; it's a philosophy rooted in the lean manufacturing principles introduced by Toyota in the 1950s. It is reshaping the construction industry by focusing on efficiency, waste reduction, and continuous improvement. Unlike traditional methods, which often lead to budget overruns and missed deadlines, lean construction maximizes value while minimizing redundancy. The Lean Construction Institute notes that 70% of construction projects face cost and time overruns, calling for a better approach to building projects. In this blog, we’ll explore the principles of lean building in the AEC industry, discuss how to implement lean practices and compare them with traditional project management methods.
Principles of Lean Building in AEC
At its core, lean construction is built on six principles, as defined by the Lean Construction Institute. These principles aim to streamline processes, enhance collaboration, and deliver better outcomes.
1. Optimize the Whole
Lean philosophy shifts the focus from isolated tasks to the entire project lifecycle. Instead of concentrating solely on individual responsibilities, teams work collaboratively to ensure that all phases interact smoothly, reducing delays and potential conflicts. A key tool in this approach is Integrated Project Delivery (IPD), which aligns owners, designers, and contractors under a single contract. This approach ensures that all parties are financially incentivized to improve outcomes and work together throughout the project.
2. Generate Value
Generating value is central to lean construction, where understanding and delivering on the client’s priorities take precedence. Value stream mapping is used to identify activities that contribute to the project’s value and eliminate those that do not. For example, examining the lifecycle of a project from design to completion helps streamline workflows, minimize unnecessary steps, and ensure that all efforts align with the client’s expectations.
3. Eliminate Waste
Waste is a significant concern in construction and can take many forms, such as overproduction, waiting, excess transportation, or defects. Lean construction addresses these inefficiencies by automating repetitive tasks and improving workflows to focus on value-adding activities. For instance, prefabrication is a common lean practice that reduces material waste while also speeding up construction timelines.
4. Focus on Flow
Maintaining a smooth and uninterrupted flow of materials, labor, and information is critical in lean construction. By ensuring that resources are available precisely when needed, disruptions and bottlenecks are minimized. This focus on flow keeps projects running efficiently and helps teams stay on schedule.
5. Respect for People
Lean construction emphasizes the importance of trust, communication, and collaboration among all stakeholders. Open dialogue and mutual respect help teams address conflicts constructively, align on shared goals, and work together more effectively. This principle recognizes that the success of a project relies heavily on the strength of its relationships.
6. Continuous Improvement
Continuous improvement is a cornerstone of lean construction. By adopting the Plan-Do-Check-Act (PDCA) cycle, teams can analyze their performance, identify constraints, and implement solutions to improve processes consistently. This ongoing refinement ensures that lean construction remains dynamic and adaptable to evolving challenges.
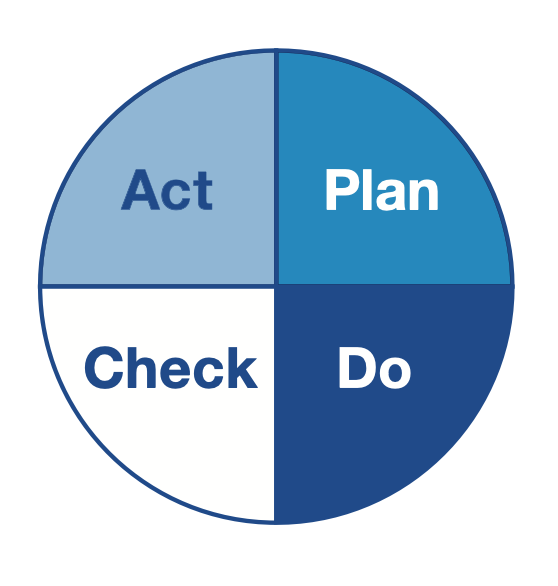
Lean Construction Tools and Techniques
To implement lean principles effectively, several methodologies and tools have been developed. Each is designed to enhance collaboration, streamline workflows, and deliver better project outcomes.
The Last Planner System (LPS)
The Last Planner System (LPS) is a collaborative scheduling approach that involves frontline workers, known as "last planners," in developing detailed and reliable schedules. By including foremen, supervisors, and project managers in the planning process, LPS ensures that daily operations are well-coordinated, reducing uncertainty and enhancing workflow reliability. Learn about the five planning elements of LPS in our blog post.
Just-In-Time (JIT)
Just-In-Time (JIT) delivery is another key methodology that ensures materials and labor arrive precisely when needed. This reduces storage costs and prevents waste, as seen in the T-30 Hotel project in China, where prefabricated parts were manufactured off-site and efficiently assembled on-site.
Big Room Planning
Big Room Planning brings all stakeholders into a shared physical or virtual space to foster collaboration. This approach eliminates the traditional hierarchical flow of decisions and creates a more inclusive environment where everyone aligns on project goals, timelines, and priorities.
Target Value Delivery (TVD)
Target Value Delivery (TVD) focuses on setting clear cost, quality, and schedule targets at the outset of a project. Teams work collaboratively to ensure these benchmarks are met, optimizing resources while maintaining alignment with the client’s vision.
BIM Integration
Finally, Building Information Modeling (BIM) integrates lean principles with digital workflows to improve efficiency. BIM reduces rework, optimizes material orders, and serves as a centralized hub for communication and data sharing. Its ability to simulate various scenarios also helps teams make informed decisions while minimizing waste and maximizing value.
Benefits of Lean Building Philosophy
Lean construction offers a wide range of benefits, making it a superior approach to traditional methods. One of its most notable advantages is cost reduction. By identifying and eliminating waste, lean practices lower project expenses related to materials, labor, and overhead. Projects with high lean intensity are 3x more likely to complete ahead of schedule and 2x more likely to stay under budget, as noted by the Lean Construction Institute.
Efficiency is another significant advantage. Lean methods streamline workflows by removing non-value-adding activities and improving coordination among teams. For example, pull planning techniques allow teams to work backward from project milestones, ensuring that every task contributes directly to the end goal. This approach can boost productivity by as much as 50%.
Collaboration is also a key focus of lean construction. By fostering open communication and mutual trust, lean practices ensure that stakeholders—including contractors, project teams, and clients—work together seamlessly. This collaborative environment makes it easier to identify and address constraints, leading to smoother project execution and better outcomes for all parties.
Other Key Benefits
- Quality Improvement: Lean construction focuses on delivering high-quality products through continuous feedback mechanisms and quality control, resulting in fewer defects and higher overall project quality.
- Safety Enhancement: Systematic safety protocols and continuous monitoring reduce workplace accidents, making the job site safer for workers.
- Environmental Impact: Lean practices support sustainability by minimizing waste and resource consumption, contributing to a more environmentally friendly construction process.
- Client Satisfaction: Projects utilizing lean construction report higher client satisfaction due to timely and budget-compliant delivery.
Lean Building Philosophy vs. Traditional Project Management
Case Studies: Construction Projects Using Lean
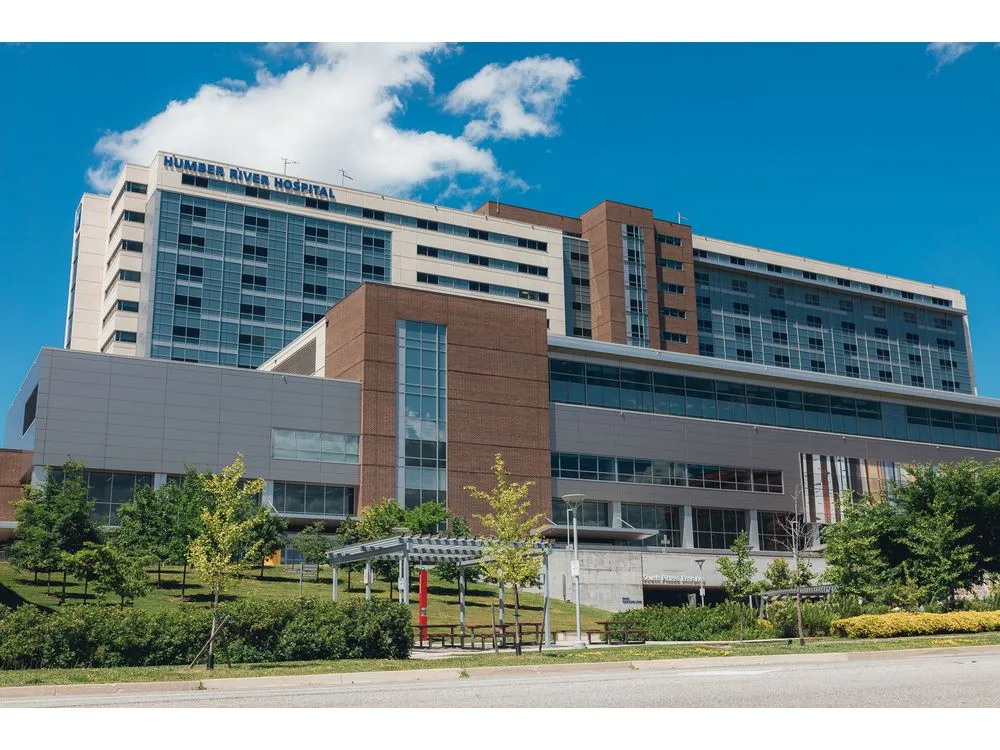
Humber River Hospital, Toronto, Canada
The Humber River Hospital is recognized as North America's first fully digital hospital, designed to enhance patient care through advanced technology and sustainable practices. The project was completed in 2015 and encompasses a 1.8 million square-foot facility with 656 beds.
Lean Construction Implementation
- Off-Site Prefabrication: The project employed lean methods by prefabricating 360 patient washrooms and 14 telecommunications/data rooms off-site.
- Waste Management: An impressive 96% of construction waste was diverted from landfills, demonstrating a commitment to sustainability.
- Energy Efficiency: The hospital achieved an annual energy use intensity (EUI) target of 348 ekWh/m², which is 47% lower than typical benchmarks for hospitals. This efficiency was supported by features such as a rainwater harvesting system expected to save 450,000 liters of potable water annually.
Outcomes
- Cost and Time Savings: The hospital opened six months ahead of schedule, resulting in significant cost savings. The total construction cost was approximately $1.75 billion.
- Sustainability Achievements: Originally targeting LEED Silver certification, the project exceeded expectations and achieved LEED Gold status due to its innovative design and sustainability measures.
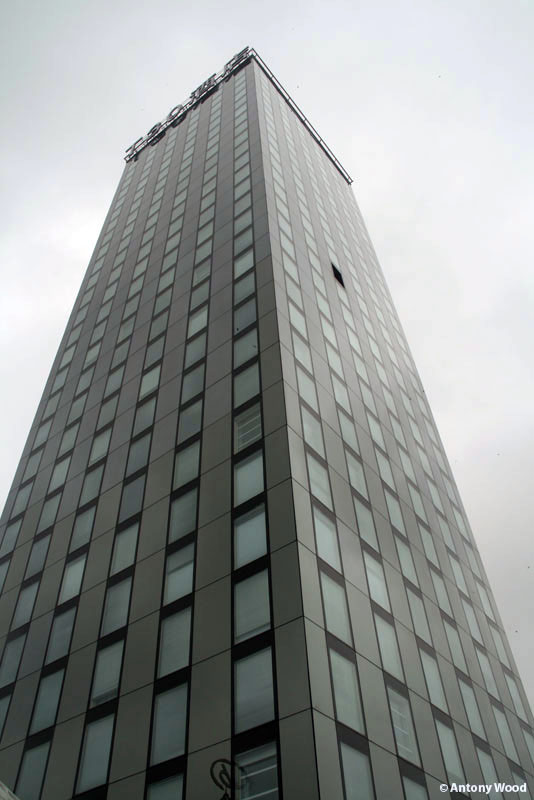
T-30 Hotel, Changsha, China
The T-30 Hotel, a 30-floor, all-steel structure, is notable for its rapid construction timeline, completed in just 15 days using lean construction techniques. This project exemplifies the potential of lean methodologies in achieving speed without compromising quality.
Lean Construction Implementation
- Modular Construction: The hotel was constructed using modular units that were prefabricated off-site.
- Just-In-Time Delivery: Materials were delivered precisely when needed, reducing storage costs and minimizing waste associated with excess inventory.
Outcomes
- Fast Track Completion: The hotel’s rapid construction timeline demonstrates the effectiveness of lean principles in accelerating project delivery without sacrificing safety or quality.
- Safety Record: Throughout the construction process, there were zero work-related injuries reported, highlighting the safety benefits of organized workflows inherent in lean practices.
Common Challenges with Lean Building Philosophy and Strategies to Overcome Them
Lean building philosophy has revolutionized construction by emphasizing efficiency, waste reduction, and continuous improvement. However, implementing these principles isn’t without its challenges. From resistance to change to technical and financial constraints, teams often face hurdles that can hinder progress. Below, we address common obstacles and strategies to overcome them.
Resistance to Change
Resistance to lean practices often stems from a fear of losing control, skepticism about benefits, or a lack of understanding. Leaders play a pivotal role in overcoming this resistance. By actively participating in lean activities, clearly communicating the vision, and engaging directly with employees, leaders can build trust and encourage buy-in. Empowering employees by involving them in decision-making and problem-solving fosters a sense of ownership, further reducing resistance.
Training Gaps
Inadequate training leads to misaligned teams and ineffective use of lean tools. To address this, companies must invest in comprehensive training programs that cover tools like the Last Planner System (LPS) and the identification of the Eight Wastes. Standardized onboarding ensures that trade partners understand the project’s lean expectations, promoting consistency across teams. Regular workshops and knowledge-sharing sessions encourage continuous learning and adaptability, helping teams sustain lean principles in dynamic environments.
Financial and Technical Challenges
Financial and technical constraints can pose significant barriers to adopting lean practices. Securing adequate funding is critical for initiatives such as hiring lean specialists, training staff, and acquiring necessary tools. Standardizing technology across teams aligns processes with lean strategies, avoiding inefficiencies and improving coordination. Additionally, using performance metrics—both quantitative and qualitative—can demonstrate the business value of lean, tracking progress and identifying areas for improvement.
Governance and Bureaucracy
Overly rigid governance structures can stifle decision-making and slow down lean implementation. To address this, organizations should adopt “just enough” governance frameworks that are flexible and efficient. Providing teams with access to critical data, such as information on delays, rework, and waste, empowers them to make informed decisions quickly. This agile approach reduces bottlenecks and accelerates project workflows.
Emerging Tools and Technologies Supporting Lean Building
Emerging tools and technologies not only enhance efficiency but also support lean principles in new and transformative ways.
AI for Construction Project Management
Lean philosophy of building involves a lot of communication, which needs to be well-documented and accessible to relevant stakeholders. AI can now automate many aspects of project documentation management, saving hours every week and preventing errors. Cogram produces meeting minutes of online and in-person (e.g., on-site and in conference rooms) meetings, directly in a firm’s custom template document. Cogram’s mobile app also allows you to take photos on-site which it can integrate with meeting minutes to produce a complete, visual site report.
Digital Twins
Digital twins—virtual replicas of physical construction sites—provide real-time insights through data collected from sensors and other sources. These tools enable continuous monitoring of construction progress, allowing teams to identify and resolve issues quickly. Predictive maintenance, informed by digital twin analysis, helps foresee potential problems and implement preventive measures, reducing downtime and improving resource allocation.
Reality Capture and 3D Scanning
Reality capture technologies, including 3D scanning, ensure accurate as-built documentation by aligning digital models with actual construction. Regular scans detect deviations from design plans, enabling prompt corrective actions. This reduces errors and fosters collaboration by providing stakeholders with a shared, accurate view of the project.
Autonomous and Smart Construction
The rise of autonomous construction technologies, including robots and 3D printers, will redefine how projects are executed. These innovations will streamline supply chains and improve cycle efficiency. Smart construction tools, connected through IoT, will passively generate data for real-time tracking and decision-making.
Lean Supply Chain Management
Efficient supply chain management will become increasingly critical. Strategic sourcing, just-in-time delivery, and strong supplier relationships will minimize inventory waste. Technologies like blockchain and IoT will enhance transparency and reliability in supply chain operations, ensuring seamless material flow.
Offsite and Modular Construction
Offsite and modular construction methods, which rely on controlled environments, reduce onsite work and improve quality control. These approaches align perfectly with lean principles, emphasizing collaboration and efficient workflows to meet deadlines and budgets.
Design for Manufacture and Assembly (DfMA)
DfMA emphasizes designing components for ease of assembly, reducing waste and labor costs. This approach simplifies onsite installation and enhances productivity, integrating seamlessly with lean practices to achieve better outcomes.
Best Resources for In-Depth Learning of Lean Construction
Here’s a curated list of valuable resources to help you begin exploring and mastering Lean Construction practices.
- Lean Construction Academy: Offers online courses on Lean Construction topics with lifetime access and certificates of completion. Suitable for individual learners and corporate training programs. Lean Construction features a blog with insightful content on Lean construction principles and practices.
- Lean Construction Institute (LCI) Guides: Provides practical guides and reports on Lean construction practices, including the Last Planner System® and Integrated Project Delivery. A key resource for implementing Lean principles in projects.
- The Lean Builder Blog: Focuses on practical lean construction tips and resources tailored for leaders in the field, providing easily applicable tools for superintendents and project managers.
- Procore Learning: Lean Construction Fundamentals: Bridges lean concepts with real-world applications. It covers essential tools like the Last Planner System and 5S Plan to enhance efficiency and reduce waste on job sites.
- Jason Schroeder (YouTube): Founder of elevateconstructionist.com, Jason shares practical insights on Lean Construction methodologies through engaging YouTube content.
- Lean Construction Education Program (LCEP) by AGC: Offers a structured curriculum, starting with a free Lean 101 course and advancing to a CM-Lean credential. Designed for professionals to master Lean principles across all levels.
- Lean Construction Certificate at FIU: A 40-hour program with weekly classes, focusing on executing construction projects using Lean principles.
Wrapping Up
Lean construction is transforming how building projects are managed, prioritizing efficiency, collaboration, and innovation. By focusing on waste reduction and continuous process improvement, it unlocks the potential for significant advancements in project outcomes. As the industry increasingly adopts digital tools, modular techniques, and sustainable practices, lean principles provide a practical framework for smarter, faster, and more resource-efficient construction. Embracing this approach enables professionals to tackle current challenges while paving the way for a more sustainable and resilient future.